Advanced Techniques in Modern Tank Welding Inspection
Comprehensive Overview to Effective Container Welding Inspection Techniques and Ideal Practices for High Quality Guarantee
In the realm of tank welding, strenuous evaluation methods are extremely important for safeguarding structural honesty and guaranteeing compliance with market guidelines. As we discover these essential elements, it becomes clear that a proactive examination approach is not simply valuable, yet crucial for functional success in atmospheres dealing with hazardous products.
Relevance of Storage Tank Welding Evaluation
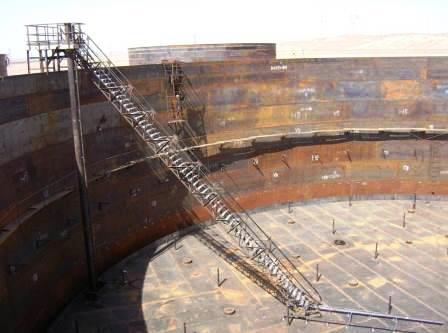
Container welding inspection acts as a preventative measure, identifying potential flaws such as cracks, porosity, or incorrect joint infiltration before they escalate into major concerns. Regular assessments not only abide by industry guidelines and criteria however additionally enhance the durability of the tanks, decreasing the demand for costly fixings or replacements.

Visual Assessment Strategies
Employing systematic visual examination techniques is essential for analyzing the quality and stability of welded joints in storage tanks. This technique acts as the very first line of protection in recognizing possible issues such as splits, damages, and not enough infiltration. The assessor needs to come close to the job with an eager eye, making use of ideal devices like multiplying glasses, flashlights, and mirrors to improve exposure.
During the evaluation process, the inspector ought to examine the weld account, ensuring it adheres to defined standards and standards (Tank Welding Inspection). This consists of examining the grain size, elevation, and fusion with the base material. Assessors must likewise pay close interest to the surrounding areas for indicators of thermal distortion or contamination that might impact the weld's performance
Documents of searchings for is necessary; examiners ought to record any kind of abnormalities, categorizing them by seriousness for further analysis. This organized method not only help in instant defect identification however also adds to long-lasting quality control by making sure conformity with sector requirements. Normal training and calibration of aesthetic evaluation techniques better boost the reliability of analyses, inevitably resulting in safer and a lot more resilient container structures.
Non-Destructive Testing Techniques
Non-destructive testing (NDT) techniques are frequently utilized in tank welding inspections to examine the stability of welded joints without jeopardizing their structural integrity. These methods are vital for determining issues such as fractures, gaps, look these up and inclusions that might lead to disastrous failings if left undiscovered.
Usual NDT methods include ultrasonic screening (UT), which utilizes high-frequency acoustic waves to identify inner imperfections; radiographic screening (RT), using X-rays or gamma rays to imagine weld frameworks; and magnetic fragment testing (MT), which reveals surface area and near-surface discontinuities in ferromagnetic products (Tank Welding Inspection). Fluid penetrant testing (PT) is likewise commonly made use of, efficient in discovering surface-breaking issues by applying a fluorescent or shade contrast color
Each NDT method has its specific applications and advantages, making it necessary for inspectors to choose the proper method based important site on the product and the kind of weld being reviewed. The integration of these NDT methods into the inspection process improves the total top quality assurance framework, making sure that welded containers meet safety and performance requirements. Eventually, NDT plays an important duty in maintaining the stability and long life of container frameworks in different commercial applications.

Documentation and Coverage
Making certain thorough documentation and coverage throughout container welding examinations is essential for keeping conformity with sector requirements and promoting reliable interaction among stakeholders. Proper documents offers as an extensive record of examination tasks, findings, and any kind of rehabilitative activities taken throughout the welding process. This information is important not only for quality control however also for audits and regulatory reviews.

A well-structured evaluation record need to consist of information such as the day of assessment, names of inspectors, welding treatments used, products utilized, and any inconsistencies from developed standards. In addition, photos and diagrams can boost the clearness of the record, giving aesthetic context to the findings. It is also vital to document any kind of non-conformities together with their resolution, ensuring that all stakeholders are educated of potential threats and the actions taken to alleviate them.
Additionally, keeping a centralized data source for all assessment reports enables for easy retrieval and testimonial, promoting a culture of openness and responsibility. By focusing on meticulous paperwork and coverage, organizations can not just copyright high quality guarantee but additionally strengthen their track record within the sector, eventually bring about boosted security and functional efficiency.
Constant Renovation Practices
Constant renovation techniques are important for improving the high quality and performance of container welding examinations. Implementing a systematic method to evaluate and fine-tune assessment methods click fosters a culture of quality control within the organization. One effective strategy involves regular training and upskilling of inspection personnel to stay abreast of the most recent welding technologies and criteria. This makes certain assessors have the needed understanding and skills to identify defects accurately.
Furthermore, utilizing data-driven evaluation enables organizations to track examination results, identify fads, and identify areas for renovation. Utilizing tools such as origin evaluation can assist in understanding the underlying concerns causing problems, making it possible for targeted interventions. Additionally, obtaining feedback from examination teams and stakeholders develops a collective environment that motivates innovative services.
Including sophisticated innovations, such as computerized evaluation systems and real-time surveillance, can substantially enhance the accuracy and rate of evaluations. Normal audits of the inspection procedures additionally add to a culture of responsibility and continual refinement. Eventually, these continual enhancement techniques not only elevate the high quality of container welding evaluations but additionally add to general functional quality and customer contentment.
Conclusion
In verdict, reliable container welding examination is crucial for making certain the architectural integrity and safety of storage systems, specifically those managing hazardous products. Utilizing a mix of visual inspection strategies and non-destructive testing methods helps with the very early recognition of issues, therefore keeping compliance with industry standards.